Table of Contents
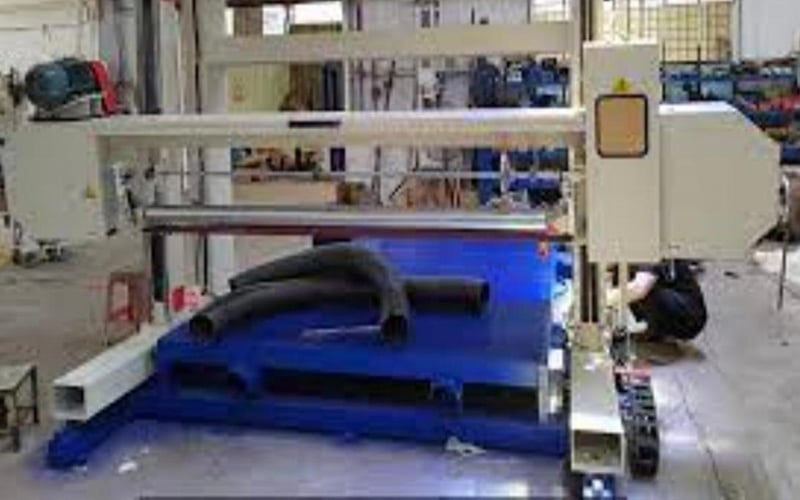
Understanding the Manufacturing Process of Sandwich Panels
When it comes to building construction or industrial applications, sandwich panels have become an increasingly popular choice due to their strength, durability, and versatility. These panels consist of two outer layers, known as facings, with a core material in between. The manufacturing process of sandwich panels involves several steps, combining different materials and techniques to create a final product that meets specific requirements. In this article, we will delve into the various aspects of manufacturing sandwich panels.
1. Selection of Materials
The first step in manufacturing sandwich panels is carefully selecting the materials to be used. The facings can be made of various materials such as metal, wood, or fiber-reinforced polymers (FRP). The core material, which provides the panel's structural integrity, can be made of materials like foam, honeycomb, or mineral wool. The selection of materials depends on factors such as desired strength, insulation properties, and fire resistance.
2. Preparation of Facings
After selecting the facings, they need to be prepared for the manufacturing process. Metal facings are typically coated with protective layers to enhance their durability and resistance to corrosion. Wood facings may require treatment to improve moisture resistance and prevent decay. FRP facings may need to undergo curing processes to achieve the desired strength and chemical resistance.
3. Core Material Integration
The core material is a crucial component of sandwich panels, providing stability and insulation properties. The chosen core material is integrated between the prepared facings using adhesives or mechanical fasteners. The integration process ensures a strong bond between the facings and the core, resulting in a cohesive panel structure.
4. Cutting and Shaping
Once the core material is integrated, the sandwich panel is cut and shaped according to the required dimensions. Sophisticated cutting techniques, such as CNC (Computer Numerical Control) cutting, are often employed to ensure precision and accuracy. The panels can be manufactured in various shapes and sizes to suit specific applications.
5. Surface Finish
After cutting and shaping, the sandwich panels undergo surface finishing processes to enhance their appearance and protect them from external factors. The type of surface finish depends on the selected materials. Metal facings may undergo painting or powder coating processes, while wood facings may be treated with varnish or sealants.
6. Edge Sealing
To ensure the longevity and performance of sandwich panels, the edges need to be sealed. This prevents moisture or contaminants from infiltrating the panel structure, which could compromise its integrity over time. The sealing process may involve applying sealants or using edge profiles specifically designed for sandwich panels.
7. Insulation Integration
In some cases, sandwich panels are required to have insulation properties. This is achieved by integrating insulation materials within the core or between the facings and the core. Insulation materials such as polyurethane foam or mineral wool can enhance thermal and acoustic insulation, making the panels suitable for applications with specific temperature or sound requirements.
8. Quality Control
Throughout the manufacturing process, quality control measures are implemented to ensure the sandwich panels meet the required standards. These measures may include dimensional checks, adhesion tests, and inspections for any defects or imperfections. Compliance with industry regulations and customer specifications is of utmost importance.
9. Packaging and Transportation
Once the sandwich panels are manufactured and pass quality control checks, they are carefully packaged to protect them during transportation. Packaging methods may vary depending on the size and fragility of the panels. Proper packaging ensures that the panels arrive at their destination in optimal condition and ready for installation.
10. Installation and Application
The final step in the process is the installation and application of sandwich panels. These panels are widely used in industries such as construction, automotive, aerospace, and cold storage. Their versatility allows them to be used for walls, roofs, floors, and partitions, providing structural strength, insulation, and aesthetic appeal.