Table of Contents
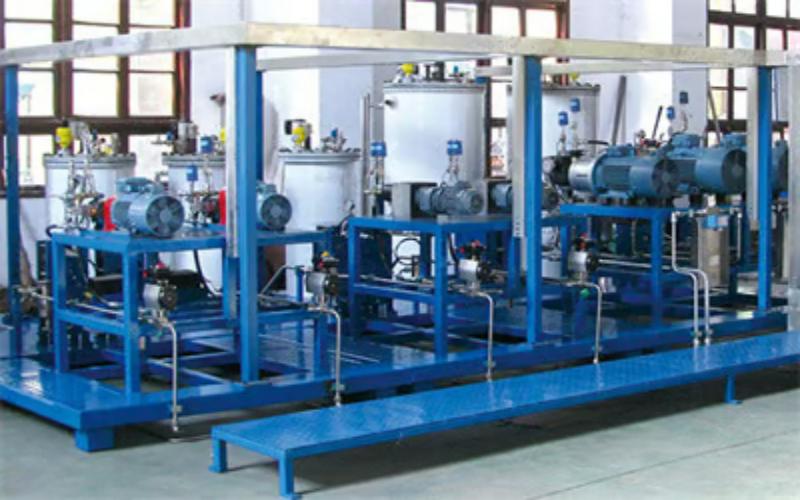
How do you manufacture sandwich panels
Introduction
Sandwich panels are versatile building materials used in various industries, including construction, aerospace, and transportation. They consist of a core material sandwiched between two outer layers, offering strength, insulation, and aesthetic appeal. This article will explore the manufacturing process of sandwich panels, shedding light on the different aspects involved.
The Core Material
The core material of sandwich panels plays a crucial role in determining their properties. Common core materials include expanded polystyrene (EPS), polyurethane foam, and mineral wool. These materials offer different levels of insulation, fire resistance, and structural integrity. The choice of core material depends on the specific requirements of the application.
Outer Layers
The outer layers of sandwich panels are typically made of materials such as aluminum, steel, fiberglass, or composite materials. These layers provide protection to the core material and contribute to the panel's overall strength and durability. The choice of outer layers depends on factors such as cost, desired aesthetics, and environmental conditions.
Bonding Process
The bonding process is a critical step in manufacturing sandwich panels. It involves applying adhesive or using mechanical fasteners to join the core material and outer layers. Adhesives such as epoxy, polyurethane, or acrylic are commonly used. The bonding process ensures a strong and durable connection between the layers, enhancing the panel's structural integrity.
Panel Formation
The panel formation process involves the assembly of the core material and outer layers. The core material is placed between the outer layers, and pressure is applied to ensure proper bonding. This can be done through various methods, including hot press molding, vacuum bagging, or continuous lamination. The chosen method depends on the specific manufacturing requirements and desired panel characteristics.
Cutting and Shaping
Once the panels are formed, they are cut and shaped according to the desired dimensions. This process can be performed using saws, routers, or water jet cutting machines. Precision cutting is essential to ensure accurate panel sizes and proper fit during installation.
Surface Finishing
Surface finishing is an important step to enhance the appearance and protect the sandwich panels from environmental factors. This can involve applying coatings, paints, or laminates to the outer layers. The chosen finishing method depends on factors such as desired aesthetics, durability, and the intended application of the panels.
Quality Control
Quality control is crucial in the manufacture of sandwich panels to ensure they meet the required standards and specifications. This involves conducting various tests, including dimensional checks, strength testing, fire resistance tests, and thermal conductivity measurements. Quality control measures help identify any defects or inconsistencies in the panels, ensuring that only high-quality products reach the market.
Applications of Sandwich Panels
Sandwich panels find applications in a wide range of industries. In construction, they are used for roofing, wall cladding, and insulation purposes. In the aerospace industry, sandwich panels are utilized for aircraft interiors, cabin partitions, and cargo containers. They are also commonly used in the automotive and marine sectors. The versatility and performance of sandwich panels make them a popular choice in many different applications.
Conclusion
Manufacturing sandwich panels involves a series of steps, including selecting the core material, bonding the layers, forming, cutting, shaping, finishing, and conducting quality control tests. The resulting panels offer strength, insulation, and aesthetic appeal, making them suitable for various industries. Understanding the manufacturing process helps in appreciating the value and versatility of sandwich panels in the modern world.