Table of Contents
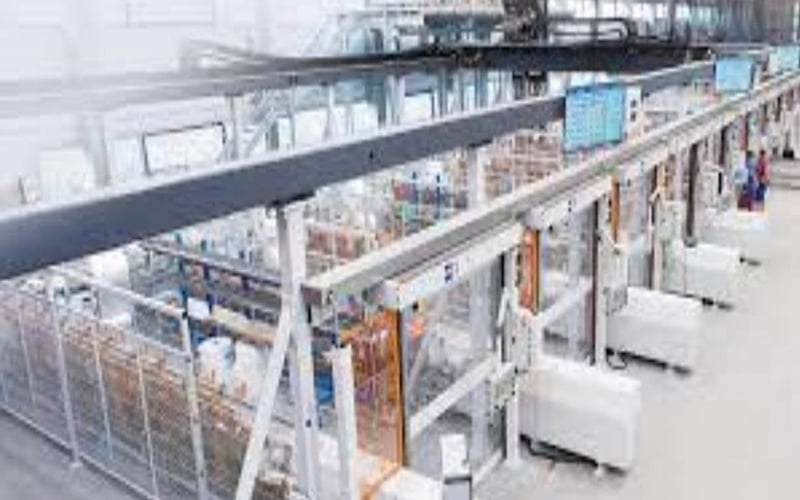
The Basics of PU Panels
PU (polyurethane) panels are a versatile building material that is widely used in various industries. These panels are known for their excellent insulation properties, durability, and ease of installation. In this article, we will explore the process of how PU panels are made and the different factors that contribute to their quality and effectiveness.
The Raw Materials
PU panels are made using a combination of two main components: polyol and isocyanate. Polyol is a viscous liquid that acts as a base material, while isocyanate is a reactive chemical that provides the necessary strength and bonding properties. These raw materials are carefully selected based on their quality and compatibility to ensure the desired characteristics of the final product.
Mixing and Reaction
Once the polyol and isocyanate are obtained, they are mixed together in a controlled environment. This process is known as the reaction, where the two components chemically bond and form a polyurethane foam. The ratio of polyol to isocyanate is crucial in determining the density and hardness of the final product. The mixing is typically done using specialized machinery to ensure accurate proportions and thorough blending.
Additives and Enhancements
In addition to the main components, various additives and enhancements are incorporated into the PU panel formulation to improve specific properties. These additives can include flame retardants, fillers, stabilizers, and pigments. Flame retardants are particularly important for applications where fire safety is a concern, while fillers and stabilizers help enhance structural integrity and dimensional stability.
Foaming Process
Once the mixture is prepared, it is ready for the foaming process. This involves injecting the liquid mixture into a mold or onto a flat surface. The mold or surface is typically made from metal or another suitable material that can withstand the heat and pressure generated during the foaming process. The mixture expands and fills the mold, forming a foam with a cellular structure.
Curing and Cutting
After the foaming process, the PU foam needs time to cure and solidify. This typically takes several hours, during which the foam undergoes a chemical reaction and hardens. Once cured, the foam is cut into panels of the desired size and shape. Cutting can be done using various methods, including sawing, slicing, or using specialized cutting machines. The precision of the cutting process is crucial to ensure uniformity and accuracy in the final panels.
Surface Treatment
After cutting, the PU panels may undergo surface treatment to achieve specific characteristics or finishes. This can involve processes such as lamination, coating, or embossing. Lamination adds a protective layer or decorative finish to the panel, while coating provides additional durability and resistance to external factors. Embossing creates textured patterns or designs on the surface, adding aesthetic appeal and grip.
Quality Control and Testing
Throughout the manufacturing process, strict quality control measures are implemented to ensure that the PU panels meet the required standards. Samples are regularly taken and tested for various parameters, including density, hardness, thermal conductivity, and fire resistance. This rigorous testing helps identify any deviations or defects and ensures that only high-quality panels are released for use.
Applications of PU Panels
PU panels find wide-ranging applications in industries such as construction, refrigeration, automotive, and aerospace. In construction, they are used for insulation in walls, roofs, and floors, offering energy efficiency and soundproofing. In refrigeration, PU panels act as excellent insulators in cold storage facilities and refrigerated trucks. The automotive industry utilizes PU panels for interior parts and panels, providing comfort and noise reduction. In aerospace, the lightweight and high-strength properties of PU panels make them suitable for aircraft interiors and components.
The Advantages of PU Panels
PU panels offer several advantages over traditional building materials. Their excellent insulation properties help reduce energy consumption and maintain a comfortable indoor environment. They are lightweight, making installation easier and reducing transportation costs. PU panels also exhibit good resistance to moisture, chemicals, and UV radiation, ensuring long-lasting performance. Additionally, their versatility and customizable features make them a preferred choice for various applications.