Table of Contents
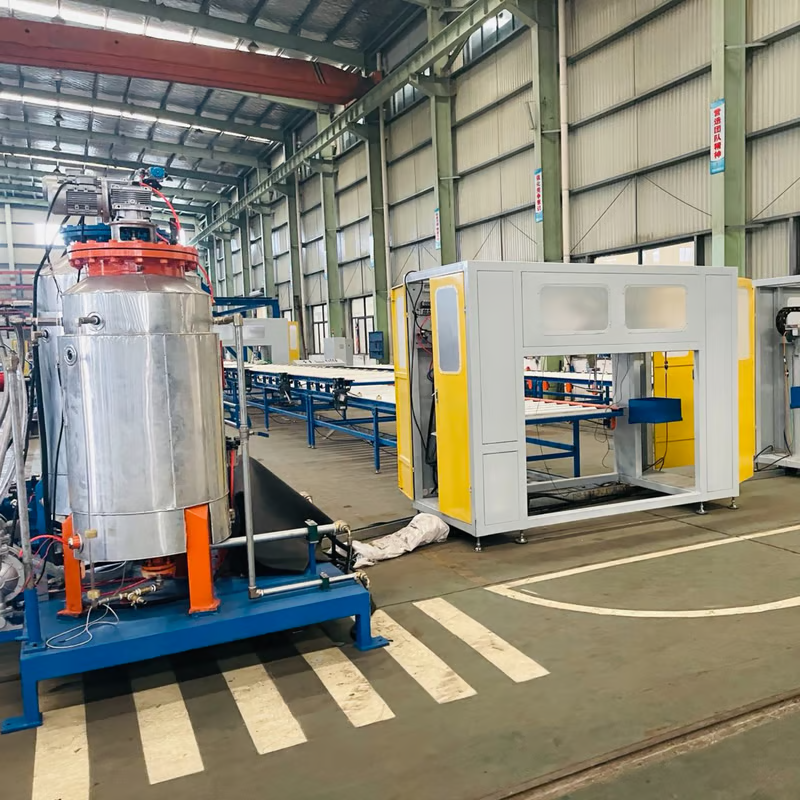
Introduction
When it comes to manufacturing sandwich panels, the process can involve many steps. One critical step involves the application of glue. This step requires precision and efficiency to ensure a strong bond between the two outer skins and the core material. One solution to improve this process is to invest in a Sandwich panel glue spraying system.
Improved Precision
A sandwich panel glue spraying system allows for precise and consistent application of glue to each panel. This technology applies glue to a specific area at a specific time, ensuring an even application and reducing the chance of errors. The use of robotics in these systems further enhances precision by ensuring the glue is applied in the correct location, on every single panel.
Faster Production Time
Traditional application methods of glue involve manually applying the adhesive to each panel. This process can be slow and unreliable. A sandwich panel glue spraying system can improve production times, as it can apply adhesive to multiple panels at one time, automatically. Additionally, the automated nature of these systems means that production times can be improved, reducing the chance of errors and reducing downtime.
Less Wastage
Manual application of glue can lead to excessive wastage, as workers may apply too much glue or not enough. The application of glue through a sandwich panel glue spraying system dramatically reduces the amount of waste generated during the production process. The automated system ensures that the exact amount of glue is applied to each panel, resulting in less waste and a more environmentally friendly production process.
Customizable Patterns
With the use of a sandwich panel glue spraying system, manufacturers have greater control over the adhesive application. A range of different patterns can be produced, allowing for a greater degree of customization of the finished product. Using different patterns also allows for further improvements to the panel’s functionality, such as improving the thermal insulation or acoustic properties.
Less Labor Required
Traditional methods for applying adhesive require workers to apply glue manually. This method is time-consuming and can be prone to errors. The use of a sandwich panel glue spraying system significantly reduces the need for manual labor. A single operator can manage the entire system automatically, allowing other workers to focus on other vital aspects of the production process.
Improved Worker Safety
A sandwich panel glue spraying system can help reduce the risk of workplace injuries in a production facility. Traditional adhesive application methods require workers to handle harmful chemicals and fumes, which can be hazardous. The use of a sandwich panel glue spraying system minimizes worker exposure to these chemicals, creating a safer work environment for all.
Lower Cost
Investing in a sandwich panel glue spraying system can be a cost-effective solution over time. As it reduces the need for manual labor, overall production costs can be reduced, even with the initial cost of the machine itself. Additionally, the reduced wastage and increased precision of adhesive application reduce material wastage, leading to further cost savings.
Remote Management Capability
Many sandwich panel glue spraying systems can be managed remotely, making it easier for operators to monitor and control the system from a distance. This feature enables efficient management of the system, even if the operator is not directly present.
Improved Quality Control
Sandwich panel glue spraying systems offer more extensive quality control than traditional adhesive application methods. The automated nature of these systems ensures that every panel is sprayed with the same amount of adhesive, reducing the chance of inconsistency or defects in the final product.