Table of Contents
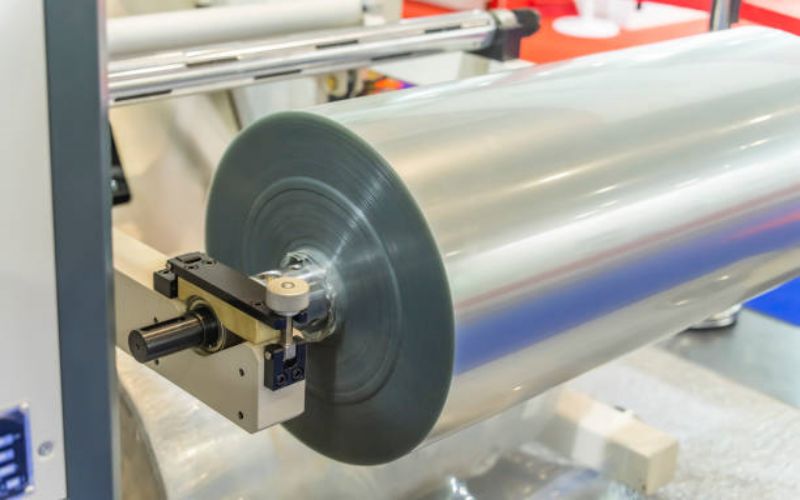
The Impact of Roll Forming Machines on Production Efficiency
Introduction:
Roll forming machines have revolutionized the manufacturing industry by increasing production efficiency and streamlining the production process. This article explores the various ways in which roll forming machines have made a significant impact on production efficiency.
1. Enhanced Precision and Accuracy
Roll forming machines offer unparalleled precision and accuracy in the production of various products. The machines are equipped with advanced technology and computer-controlled systems that ensure consistent and precise product dimensions. This level of accuracy leads to reduced errors and waste, ultimately improving production efficiency.
2. High Production Speed
One of the most significant impacts of roll forming machines on production efficiency is their ability to operate at high speeds. These machines can quickly process materials and form them into desired shapes, significantly reducing production time. The high production speed allows manufacturers to meet tight deadlines and fulfill customer orders promptly.
3. Cost-Effective Production
Roll forming machines offer a cost-effective solution for manufacturing various products. These machines enable mass production, reducing labor costs and minimizing material waste. By optimizing production efficiency, manufacturers can produce more products with minimal resources, resulting in cost savings and increased profitability.
4. Versatility and Flexibility
Roll forming machines are highly versatile and can be used to produce a wide range of products across different industries. These machines can easily switch between different product configurations and dimensions, making them ideal for custom production requirements. The ability to adapt quickly to changing production needs enhances overall production efficiency.
5. Consistent Product Quality
Roll forming machines ensure consistent product quality throughout the production process. The machines are designed to provide uniform shaping and forming, resulting in products with consistent dimensions and structural integrity. This level of consistency eliminates the need for rework or product rejection, saving valuable time and resources.
6. Reduced Manual Labor
Prior to the advent of roll forming machines, many production processes required significant manual labor. These machines have automated various tasks, minimizing the need for manual intervention and reducing labor costs. By reducing reliance on manual labor, manufacturers can allocate resources to more critical tasks, further improving production efficiency.
7. Improved Safety Measures
Roll forming machines incorporate advanced safety features to protect operators and workers. These safety measures include emergency stop buttons, interlocks, and safety guards, among others. By ensuring a safe working environment, roll forming machines minimize the occurrence of accidents and injuries, leading to uninterrupted production and improved efficiency.
8. Streamlined Production Workflow
Roll forming machines integrate seamlessly into the production workflow, allowing for a streamlined and efficient manufacturing process. These machines can be synchronized with other production equipment, such as material handling systems and automated packaging lines. The integration of roll forming machines optimizes the overall production workflow, minimizing bottlenecks and maximizing efficiency.
9. Minimized Material Waste
Roll forming machines are designed to minimize material waste during the production process. The machines utilize precise measurements and cutting techniques to ensure minimal scrap material. By reducing material waste, manufacturers can maximize resource utilization and minimize production costs, ultimately improving production efficiency.
10. Scalability and Expansion
Roll forming machines offer scalability and expansion opportunities for manufacturers. These machines can accommodate increased production volumes and adapt to changing market demands. This scalability ensures that production efficiency remains high even when there is a need for increased output, allowing manufacturers to seize growth opportunities without compromising on quality or efficiency.