Table of Contents
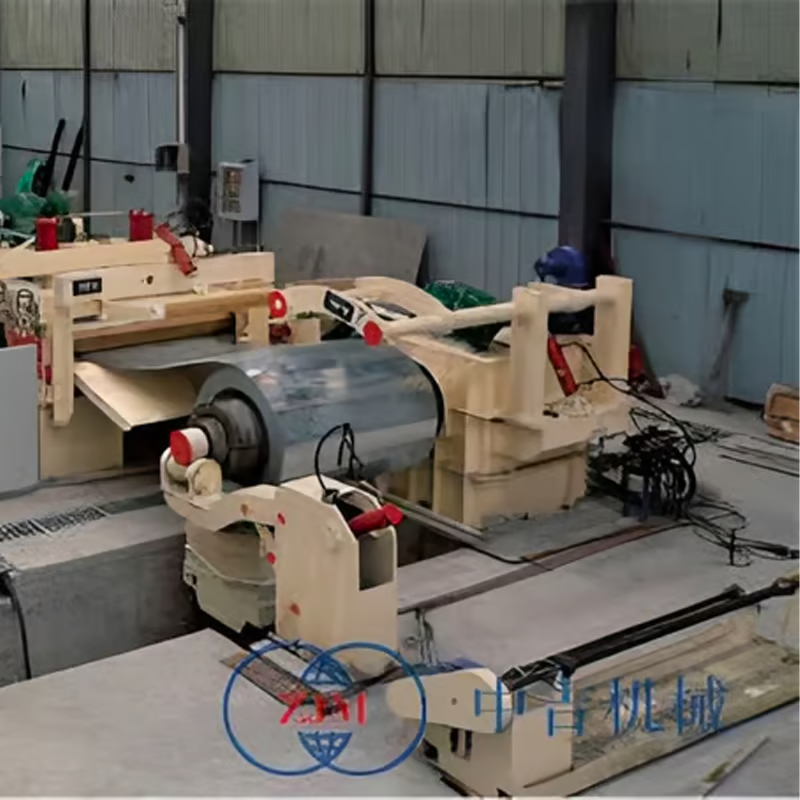
The Basics of a Cut to length line
A cut to length line (CTL) is a machine used to cut sheet metal, coils, steel, or aluminum into a desired length. The machine works by unrolling a coil or a flat sheet into a straight line, where it then goes through a leveling and feeding system before reaching the cutting blade. CTLs are designed to make the cutting process more precise and efficient, and they can take on a variety of different materials and profiles.
The Importance of a CTL
CTLs are critical in industries that require precise and consistent cuts of material, such as in the automotive, HVAC, and construction sectors, among others. With a CTL, material can be cut to exact measurements, which is necessary for manufacturing a wide range of products. CTLs can process large volumes of material at high speeds, and the automation allows for higher productivity rates and reduced downtime.
The Components of a CTL
A typical CTL includes several different components, including an uncoiler, straightener, feeder, and cutting system. The uncoiler is used to hold and unroll the material, while the straightener ensures that the material is flat and even. The feeder system precisely feeds the material into the cutting system, which then cuts the material to the desired length. Other components may be included as well, depending on the specific application.
The Benefits of a CTL
The benefits of using a CTL are significant. CTLs reduce the need for manual labor, which in turn reduces the chances of human error. They also increase production rates and decrease production times, saving manufacturers both time and money. The precise cuts that a CTL provides can also reduce waste, as there is less material being cut away than with manual cutting. Overall, a CTL is an efficient and cost-effective way to cut materials.
The Importance of Choosing the Right CTL
Choosing the right CTL is crucial for the success of any manufacturing operation. The right CTL will streamline production, produce precise cuts, and avoid costly errors. When choosing a CTL, it's important to consider the materials being cut, the production rate needed, and the desired level of automation. A CTL that is too small, too slow, or not automated enough can end up costing manufacturers time and money in the long run.
The Maintenance of a CTL
Maintenance is an essential part of keeping a CTL running smoothly. Regular cleaning, oiling, and tightening of screws and bolts can help prevent breakdowns and extend the life of the machine. It's also important to regularly inspect the machine for wear and tear, and to replace any parts that are damaged or worn. Training operators on proper use and maintenance can also help reduce errors and prevent unnecessary downtime.
The Safety Considerations of a CTL
It's important to keep safety in mind when using a CTL. Operators must be properly trained on how to use the machine and be aware of its potential hazards. Safety devices, such as guardrails, light curtains, and emergency stop buttons should be installed to prevent accidents. Operators should also wear protective gear, such as safety glasses, gloves, and earplugs, when using the machine to reduce the risk of injury.
Future Prospects of CTL
The future of CTLs is promising, as manufacturers continue to seek out more efficient and cost-effective cutting methods. Automation and robotics are expected to play a larger role in CTLs, as well as the introduction of more eco-friendly technology. The development of newer and more advanced materials will also require CTLs that can handle higher cutting speeds and offer more precise cuts.
The Different Types of CTL
There are several different types of CTLs available depending on the specific needs of a manufacturing operation. Straight CTLs are designed for cutting sheet metal, while rotary CTLs are used for cutting coil materials. Multi-blanking CTLs can cut multiple sheets or coils at once, while heavy-duty CTLs can handle thicker, heavier materials. It's important to choose the right CTL for the job to ensure maximum efficiency and precision.
The Cost of a CTL
The cost of a CTL can vary based on the specific needs of a manufacturing operation. The price can range from tens of thousands of dollars for a basic model to several hundred thousand dollars for a more advanced model. However, the cost of a CTL is often outweighed by the benefits it provides in increased productivity, reduced waste, and improved product quality.