Table of Contents
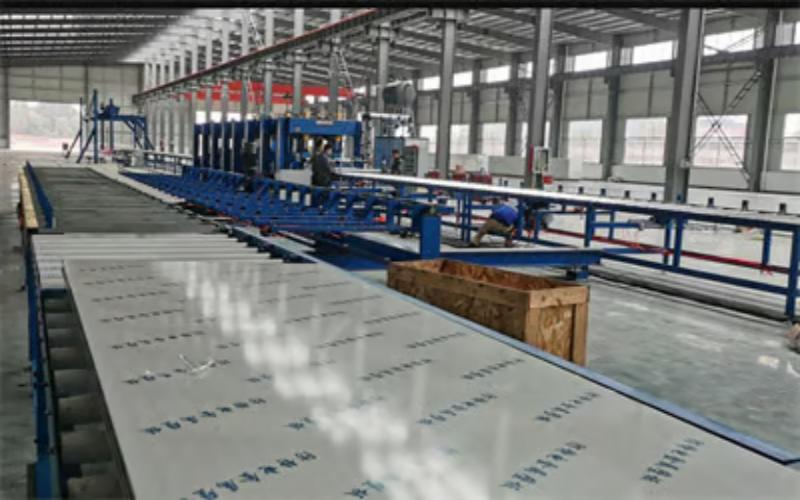
The Basics of EPS Machine
Expanded Polystyrene (EPS) machines are widely used in the manufacturing industry to produce lightweight and versatile foam products. These machines play a crucial role in the production of packaging materials, insulation boards, and various other applications. In this article, we will explore the different aspects of EPS machines, their working principles, applications, and benefits.
Understanding EPS Machine: How Does it Work?
EPS machines are designed to process polystyrene beads into expanded foam products. The process involves four primary stages: pre-expansion, molding, drying, and cutting. In the pre-expansion stage, the polystyrene beads are heated and expanded using steam, resulting in the formation of foam beads. These foam beads are then molded into the desired shape using steam and pressure in the molding stage. After molding, the foam products go through a drying process to remove excess moisture. Finally, the cutting stage shapes the foam products into their final form.
Applications of EPS Machine
EPS machines find extensive use in various industries due to the versatility of the foam products they produce. Some common applications of EPS machines include:
- Packaging: EPS machines are widely used to produce packaging materials such as boxes, trays, and containers due to their lightweight and shock-absorbing properties.
- Insulation: EPS foam is an excellent thermal insulator, making it ideal for insulation boards used in construction, refrigeration, and cold storage applications.
- Floatation Devices: EPS foam is often used in the construction of floatation devices, such as life jackets, surfboards, and buoys, due to its buoyant properties.
- Decorative Elements: EPS foam can be easily molded into various shapes and sizes, making it a popular choice for creating decorative elements like architectural moldings and sculptures.
The Benefits of EPS Machine
EPS machines offer several advantages that make them a preferred choice for foam product manufacturing:
- Cost-effective: EPS machines allow for efficient production of foam products at a relatively low cost, making them economically viable for both small and large-scale production.
- Lightweight: Foam products produced by EPS machines are lightweight, making them easy to handle, transport, and install.
- Durable: EPS foam products have excellent durability and can withstand various environmental conditions, including moisture and temperature fluctuations.
- Energy-efficient: The manufacturing process of EPS foam products consumes less energy compared to other materials, making it an environmentally friendly choice.
- Customizability: EPS machines allow for easy customization of foam products, enabling manufacturers to meet specific design and size requirements.
Choosing the Right EPS Machine
When selecting an EPS machine for your manufacturing needs, there are a few key factors to consider:
- Capacity: Determine the required production capacity based on your anticipated output and choose a machine that can meet those requirements.
- Automation: Consider the level of automation needed for your production process. Fully automated machines offer higher efficiency and productivity.
- Quality: Ensure that the machine you choose produces foam products of consistent quality and meets industry standards.
- After-sales Support: Opt for a machine from a reputable manufacturer who offers reliable after-sales support, including maintenance and spare parts availability.
Maintaining EPS Machines
To ensure the longevity and optimal performance of your EPS machine, regular maintenance is crucial. Some key maintenance tasks include:
- Cleaning: Regularly clean the machine to remove any residue or build-up that may affect its performance.
- Lubrication: Apply lubricants to the moving parts of the machine to reduce friction and prevent wear and tear.
- Inspections: Periodically inspect the machine for any signs of damage or malfunction and address them promptly.
- Training: Provide proper training to the machine operators to ensure safe and efficient operation.
The Future of EPS Machines
The demand for EPS foam products continues to grow, driven by their numerous applications and benefits. As a result, the development of EPS machines is focused on improving efficiency, automation, and sustainability. The future of EPS machines will likely involve advancements in energy-saving technologies, enhanced automation capabilities, and the use of eco-friendly materials.
In Conclusion
EPS machines are essential in the production of versatile and lightweight foam products. They find applications in packaging, insulation, floatation devices, and decorative elements. The benefits of EPS machines include cost-effectiveness, lightweight, durability, energy-efficiency, and customizability. When choosing an EPS machine, consider factors such as capacity, automation, quality, and after-sales support. Regular maintenance and proper training are necessary to ensure the optimal performance and longevity of the machine. As the demand for EPS foam products continues to rise, the future of EPS machines will focus on efficiency, automation, and sustainability.