Table of Contents
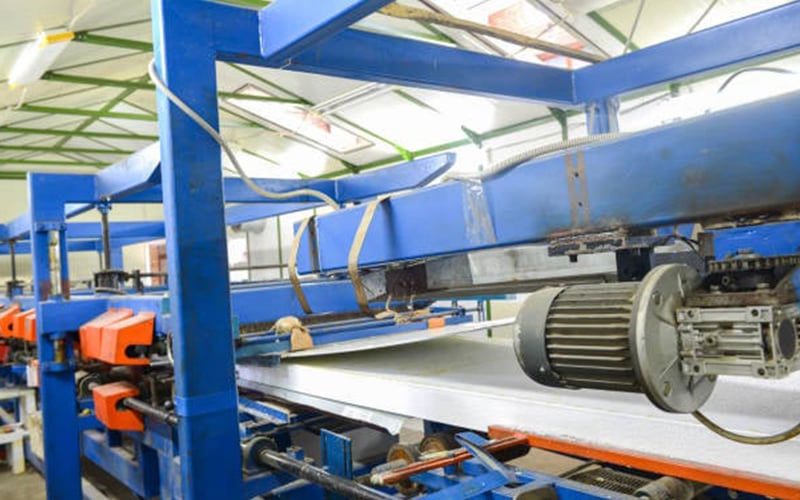
what is sandwich panel lines: A Comprehensive Guide
Sandwich panel lines are innovative manufacturing systems designed for the production of sandwich panels. These panels consist of two outer layers, known as facings, and a core material sandwiched in between. The facings can be made of various materials such as steel, aluminum, or composite materials, while the core material is typically made of foam, honeycomb, or mineral wool.
The Importance of Sandwich Panel Lines
Sandwich panel lines play a crucial role in various industries, including construction, automotive, aerospace, and refrigeration. These panels offer exceptional thermal insulation, fire resistance, and structural stability, making them highly desirable for a wide range of applications. The sandwich panel lines enable efficient and precise manufacturing of these panels on a large scale, meeting the growing demand for high-quality and cost-effective construction materials.
Components of Sandwich Panel Lines
A typical sandwich panel line consists of several key components that work together to produce sandwich panels. These components include:
1. Uncoiler
The uncoiler is responsible for unwinding the coil of the facing material, which is typically a metal sheet, before it enters the panel production process.
2. Roll Forming Machine
The roll forming machine shapes the facing material into the desired profile. This machine consists of a series of rollers that gradually bend the metal sheet to the required shape.
3. Gluing and Pressing Unit
The gluing and pressing unit is where the core material is applied between the two facings. Adhesive is applied to the facings, and the core material is inserted and pressed firmly to ensure proper bonding.
4. Cutting System
The cutting system is responsible for cutting the sandwich panels to the desired length. This can be done using various cutting methods, including saw cutting, guillotine cutting, or flying saw cutting.
5. Stacking and Packaging Unit
After the panels are cut to size, they are stacked and packaged for transportation. This unit ensures that the panels are properly organized and protected during shipping.
The Advantages of Sandwich Panel Lines
Sandwich panel lines offer several advantages for both manufacturers and end-users:
1. Efficient Production
By automating the manufacturing process, sandwich panel lines allow for efficient production, reducing labor costs and increasing productivity.
2. Customization Options
Sandwich panel lines can be easily adjusted to produce panels with different dimensions, profiles, and materials, providing flexibility for various construction projects.
3. Consistent Quality
With precise control over the production process, sandwich panel lines ensure consistent quality in each panel, minimizing variations and defects.
4. Energy Efficiency
The excellent thermal insulation properties of sandwich panels contribute to energy efficiency, reducing heating and cooling costs in buildings.
5. Versatility
Sandwich panels are suitable for a wide range of applications, such as wall cladding, roof systems, cold storage, and industrial enclosures, making them a versatile choice for construction projects.
Conclusion
Sandwich panel lines are advanced manufacturing systems that facilitate the efficient and precise production of sandwich panels. These panels offer numerous benefits, including thermal insulation, fire resistance, and structural stability. With the ability to customize dimensions, profiles, and materials, sandwich panel lines have become an essential component in the construction industry. Whether used in commercial buildings, residential properties, or industrial facilities, sandwich panels contribute to energy efficiency and provide versatile solutions for modern construction needs.