Table of Contents
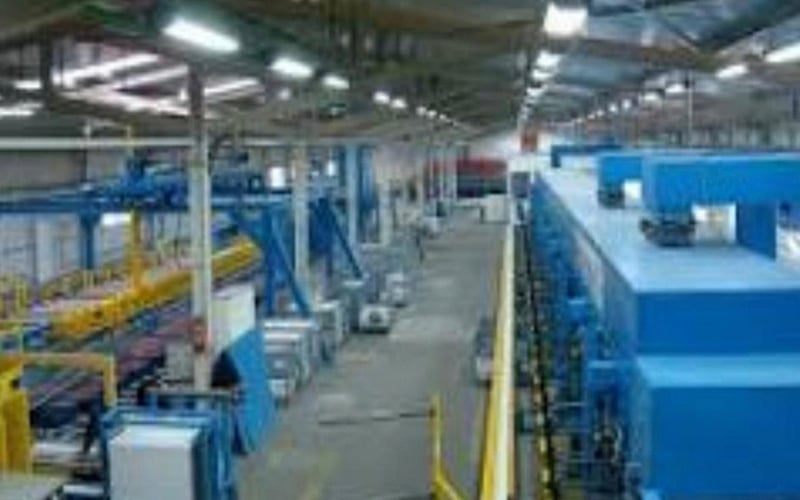
The Basics of Sandwich Panel Production Line
When it comes to constructing buildings and structures, sandwich panels have become a popular choice due to their durability, insulation properties, and cost-effectiveness. But have you ever wondered how these panels are produced? In this article, we will delve into the fascinating world of sandwich panel production lines and explore the various aspects of this innovative manufacturing process.
What are Sandwich Panels?
Before we dive into the details of the production line, let's first understand what sandwich panels actually are. Sandwich panels, also known as composite panels, are structural panels consisting of three layers - a core material sandwiched between two outer layers, often made of metal or composite materials. The core material can vary depending on the specific application, but it is usually made of materials such as expanded polystyrene (EPS), polyurethane (PU), or mineral wool.
The Role of Sandwich Panel Production Line
A sandwich panel production line is a specialized machinery setup designed to manufacture sandwich panels in a systematic and efficient manner. This production line plays a crucial role in the entire manufacturing process, ensuring the panels are produced with precision and consistency.
Components of a Sandwich Panel Production Line
A typical sandwich panel production line consists of several key components, each serving a specific purpose:
1. Uncoil and Leveling Machine
This machine uncoils the metal coils, which will serve as the outer layers of the sandwich panel. It also ensures that the metal coils are properly leveled before further processing.
2. Roll Forming Machine
The roll forming machine shapes the outer layers of the sandwich panel according to the desired profile. It can create various profiles, such as corrugated, trapezoidal, or flat, depending on the specific requirements.
3. Gluing and Pressing Machine
This machine is responsible for applying adhesive, such as polyurethane or epoxy, onto the core material. It then presses the core material and the outer layers together, ensuring a strong bond.
4. Cutting Machine
Once the sandwich panel has been pressed and bonded, the cutting machine trims the panel to the desired length. It ensures accurate and clean cuts, resulting in panels of uniform size.
5. Stacking and Packing Machine
The stacking and packing machine is the final component of the production line. It stacks the finished sandwich panels and prepares them for shipping or storage. This machine ensures efficient handling and protects the panels from damage.
The Advantages of Sandwich Panel Production Line
The use of a sandwich panel production line offers several advantages:
1. Increased Efficiency
By automating the manufacturing process, a production line significantly improves efficiency compared to manual production methods. This results in higher productivity and shorter production times.
2. Consistent Quality
A production line ensures consistent quality throughout the manufacturing process. Each panel is produced with the same precision and adherence to specifications, minimizing variations and defects.
3. Cost-effectiveness
With streamlined production and reduced labor requirements, a sandwich panel production line helps to lower production costs. This makes sandwich panels a cost-effective option for various construction projects.
4. Flexibility
A production line can be easily adapted to produce different types and sizes of sandwich panels. This allows manufacturers to cater to a wide range of customer requirements and market demands.
Conclusion
As we have explored, a sandwich panel production line is an integral part of the manufacturing process for sandwich panels. It ensures the efficient and consistent production of these versatile building materials. By understanding the intricacies of the production line, we can appreciate the technology and precision that goes into creating these durable and energy-efficient panels.